Screw Jacks are versatile pieces of equipment used to lift and lower heavy loads, making them popular choices in various industries for assembly, repair and adjustment of heavy machinery and vehicles.
Screw jacks can be driven either by motor or hydraulic fluid, depending on their application. They typically provide more energy-efficiency at high load levels than competing technology solutions.
Advantage: Self-locking
Screw jacks are mechanical components designed to convert rotary motion into linear movement, used for pushing, pulling, tensioning, locking/unlocking/tilting pivoting rolling or lifting loads from several kg up to several tonnes.
They provide a cost-effective alternative to pneumatic and hydraulic systems in areas with strict safety requirements and legislation, from small tyre-changing jacks to aircraft horizontal stabilisers.
Self-locking jacks are designed to remain stationary even when power to the system is switched off, preventing backdriving under load and eliminating the need for brakes in certain scenarios.
Single start trapezoidal lead screw drives and high helix threads can be designed as self-locking mechanisms, similar to some worm gear jacks; their flank angle and sliding friction prevent their leads from moving without external forces being applied.

Disadvantage: Limited lifting capacity
Screw jacks may seem limited when compared with hydraulic systems, which is frustrating for motion system designers. Unfortunately, they’re often disregarded as an effective means of creating controllable linear motion – though there are certain advantages they do provide.
They provide cost-effective solutions for many applications, providing reduced maintenance requirements and reliable performance. In particular, they excel at heavy-duty lifting/lowering applications like vehicle impact barriers.
These jacks feature a worm gear configuration to convert energy from motor or manual input into lifting and lowering motion, with several gear ratio options to optimize travel speed and torque optimization for specific applications.
Advantage: Simple design
Simple screw jack designs offer engineers an effective and straightforward means of lifting and positioning loads. Engineers typically opt for basic models which combine a worm gear set, threaded lead screw and guide system (rails, rollers or linear bearings).
Simple designs provide many advantages, including being easily adaptable to various applications. Because some systems may be more complex than others, however, it’s crucial that you work with an experienced distributor in order to specify the most suitable product for your specific situation.
There are various kinds of screw jacks on the market, and each variety offers specific advantages. Some models feature self-locking mechanisms which make installation, programming and tuning much simpler.
Environmentally friendly since they don’t rely on high-pressure oil leakage and can provide more efficiency and safety than pneumatic or hydraulic systems, electric pumps offer numerous other advantages over pneumatic or hydraulic ones.
Disadvantage: High cost
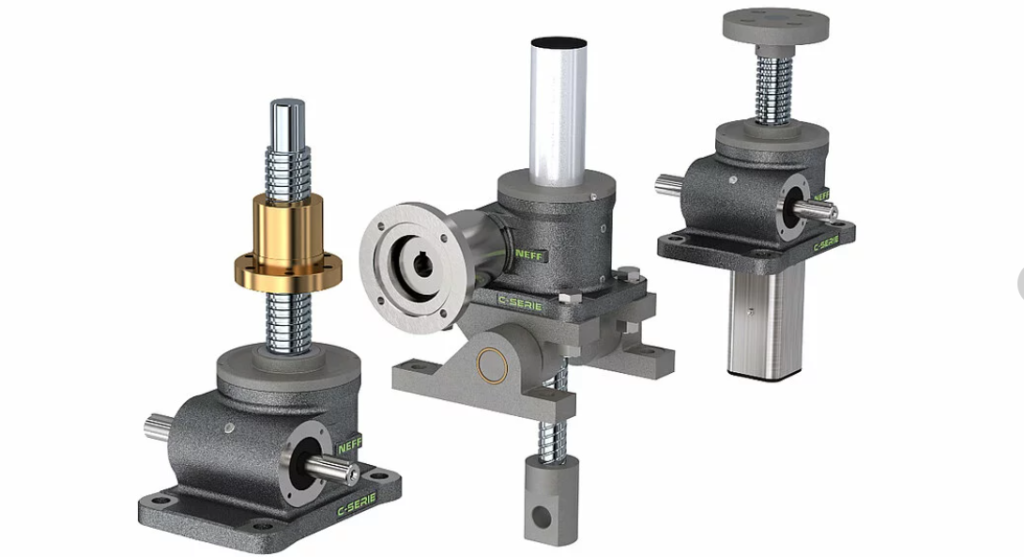
Screw jacks provide an economical and effective solution for supporting loads, whether individually or synchronized motorized arrangements with driveshafts and gearboxes for precise positioning.
Screw jacks have numerous advantages over pneumatic or hydraulic jacks, including lower maintenance costs and footprint savings, no hazardous fluids necessary, and potential shock loading risks that must be carefully considered. However, their limitations and potential for shock loading should also be carefully considered.
Under extreme shock conditions, both machine and ball screw jacks may temporarily exceed their rated capacity by around 10 percent for dynamic loads and 30 percent for static loads.
Anti-backlash screw jacks and stainless steel jacks with carbon steel load bearings on top and bottom can help avoid these issues, while sealed gear cavities on these models keep water out of their gears, making them suitable for harsh environments.